Comprehensive Analysis on Selection of Low-NOx Burners for Heaters in Petrochemical Industry
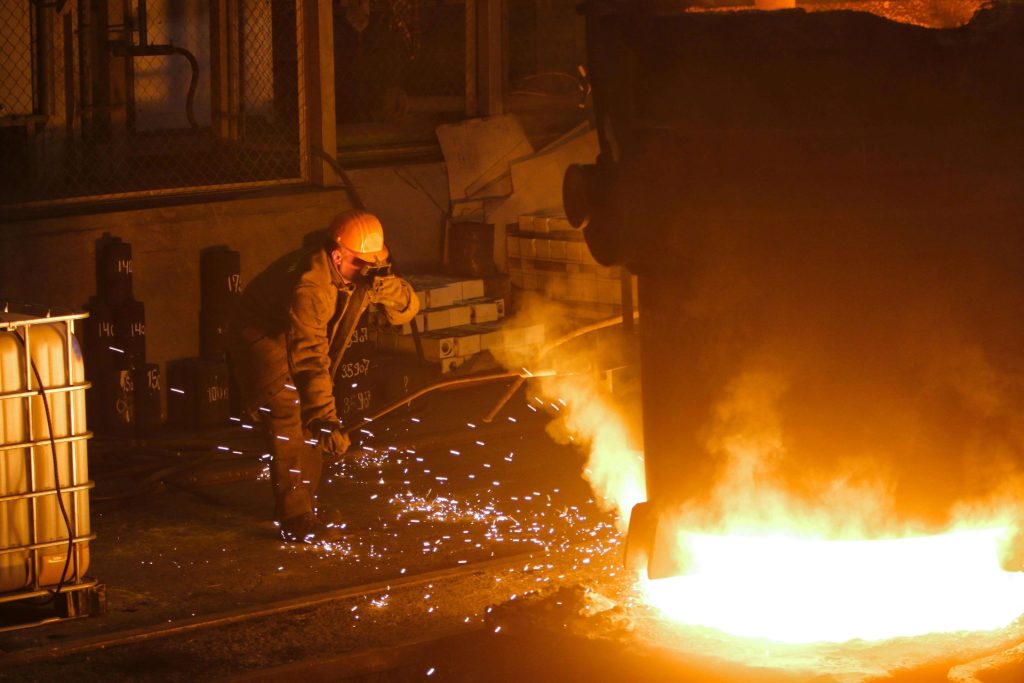
Under the "Dual Carbon" goals, the environmental retrofit of heaters in the petrochemical industry has become imperative. For instance, after retrofitting a crude distillation unit heater in a 10-million-ton refinery with low-NOx technology, nitrogen oxide (NOx) emissions dropped from 180 mg/m³ to 45 mg/m³, fuel consumption decreased by 2.3%, and annual carbon emissions were reduced by approximately 6,500 tons. These figures highlight that low-NOx burners are not merely environmental devices but also critical equipment for enhancing energy efficiency. This article delves into the scientific selection of low-NOx burners for heaters from three perspectives: technical principles, selection criteria, and application strategies.
1.Principles of Low-NOx Combustion Technologies and Applicable Scenarios
Staged Combustion Technology creates fuel-rich and lean-oxygen zones to delay combustion reactions. For example, in an ethylene cracking furnace, flame temperature was reduced by 150°C, and NOx generation decreased by 40% through air staging. This technology suits natural gas heating systems with stable fuel composition but struggles with fuel calorific value fluctuations exceeding 10%.
Flue Gas Recirculation (FGR) mixes 15–30% of flue gas into combustion air. A reforming heater using FGR reduced oxygen content from 3.5% to 2.1%, flattening temperature gradients in the combustion zone. However, when fuel sulfur content exceeds 50 ppm, risks of dew-point corrosion rise significantly.
Premixed Combustion Technology achieves precise air-fuel ratios (e.g., λ = 1.02 in an aromatics unit heater), boosting combustion efficiency to 99.6%. However, it demands strict fuel pressure stability—pressure fluctuations beyond 5% may cause flashback.
2.Systematic Analysis of Key Selection Factors
Fuel Characteristics: For vacuum residue with 0.5% sulfur content, staged combustion is preferred to avoid FGR-induced low-temperature corrosion. A refinery processing high-hydrogen (85%) gas successfully mitigated flashback risks using premixed combustion with water-cooled burner throats.
Furnace Structure Compatibility: A vertical cylindrical heater using swirl burners achieved 92% flame-to-radiant-surface alignment, improving thermal efficiency by 1.8% compared to conventional axial burners. Box-type heaters with insufficient convection section height should adopt flat-flame burners to prevent tube erosion.
Economic Evaluation: A hydrocracker burner retrofit case revealed that while selective catalytic reduction (SCR) had 30% lower upfront costs, its 5-year lifecycle costs exceeded staged combustion + FGR by 12% due to catalyst replacement. Net present value (NPV) analysis over 20 years is recommended.
3.Engineering Strategies and Innovation Trends
Hybrid Technologies are now mainstream. A 10-million-ton refinery achieved ultra-clean emissions (NOx < 30 mg/m³, ammonia slip < 3 ppm) using "staged combustion + internal flue gas recirculation + micro-ammonia injection." Intelligent control systems dynamically adjust combustion air ratios via real-time furnace temperature mapping, limiting fluctuations to ±1.5%.
Advanced Materials are breaking barriers. A pilot project using silicon carbide ceramic burner heads (1,600°C tolerance) and 3D-printed swirlers extended fuel residence time by 0.3 seconds, achieving 99.92% combustion completeness. Digital twin technology shortened field commissioning by 40% in one project.
Emerging Technologies: Plasma-assisted combustion has shown promise in trials, reducing flame zone temperatures by 200 K and NOx generation by 60% through non-equilibrium ionization. This disruptive approach may become the next-generation ultra-low-NOx solution.
Under the petrochemical industry’s high-quality development mandate, selecting low-NOx burners transcends equipment procurement—it is a systematic engineering challenge integrating process optimization, energy management, and smart controls. Enterprises should establish multidisciplinary teams (process, equipment, environmental, automation) and adopt numerical simulation coupled with field trials for plant-wide retrofits. Future advancements in combustion diagnostics, AI algorithms, and novel materials will drive low-NOx technologies toward adaptability, self-optimization, and near-zero emissions.